WASTE SORTING LINE

Annually, the globe generates over 2 billion metric tons of municipal solid waste (MSW), a figure that’s on the rise. This waste encompasses the daily refuse from households and can extend to include disposals from commercial and public sectors, varying by location. Our innovative sensor-based sorting technology has transformed the way material recovery facilities and waste management companies handle MSW, facilitating a shift towards a circular economy. Our state-of-the-art systems for sorting MSW excel in segregating a variety of materials such as plastics, paper, glass, organics, and other inert substances, along with oversized objects, from intricate mixed waste compositions.
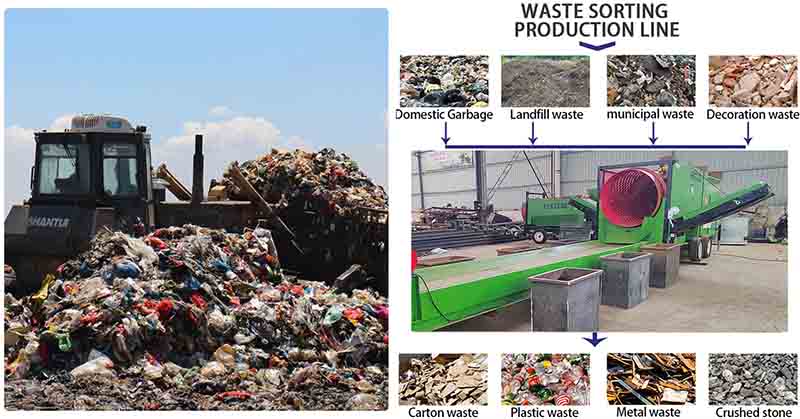
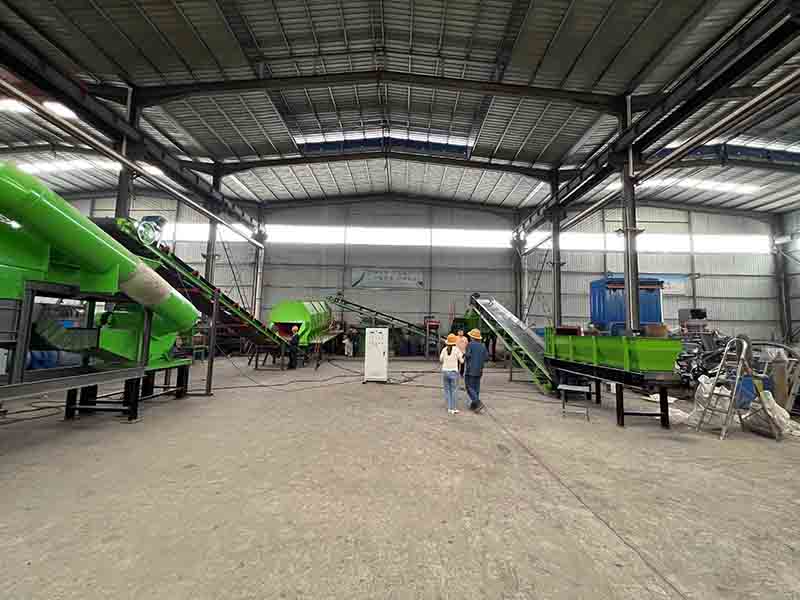
Typically, a comprehensive waste separation system comprises various components such as a plate feeder, material distribution unit, rotary screening device, air separator, magnetic separator, and a manual sorting station, among others. This system is capable of processing up to 50 tons of waste per day. Due to the considerable space required for the operation of a trash sorting facility, clients must ensure they have adequate room to accommodate the recycling setup. We highly recommend housing the system within a workshop to protect the environment and maintain the cleanliness of the surrounding area, as opposed to situating it in an open space.
How to Sort Trash – Trash Sorting Process
Upon arrival at the waste transfer station, all collected garbage is moved into the workshop, where it is initially deposited onto a plate feeder. This feeder then transfers the waste to a material distribution mechanism located at its end, ensuring an even spread of waste across the conveyor belt.
The conveyor belt transports the waste to a manual sorting area, where workers remove large, bulky items such as quilts, big branches of wood, and hazardous materials by hand.
Subsequently, the remaining waste proceeds to a rotary screening device. To facilitate smoother operation in subsequent stages, a bag breaker may be employed to tear open plastic bags before they reach the screening apparatus.
The rotary screening machine then separates the waste, using screens with 50 mm holes to distinguish between oversized and undersized materials.
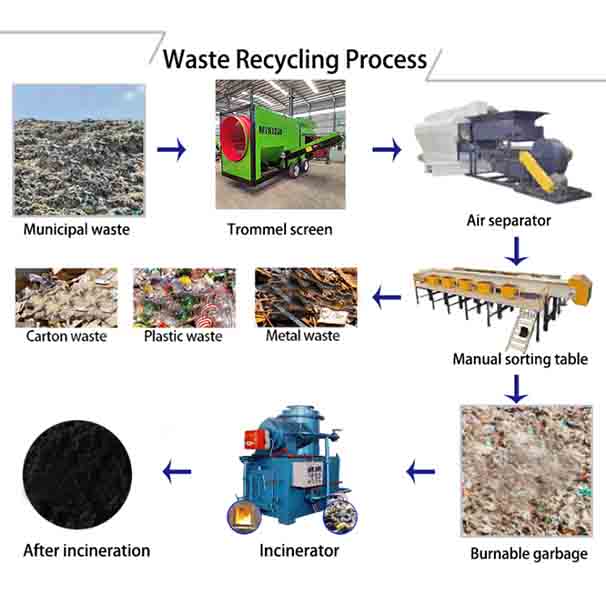
The undersized fraction, primarily organic material smaller than 50 mm in diameter, is directed through a magnetic separator to remove any ferrous objects, after which it is gathered, packaged, and removed from the facility. Oversized waste is also passed through a magnetic separator to extract metal items such as iron cans. The remaining oversized waste is then sent to a comprehensive winnowing system, which sorts the waste into light plastics, heavier materials, and miscellaneous debris.
Light plastic items are routed back to the manual sorting area, where workers remove any non-plastic elements. These cleaned plastics are then conveyed to a packaging machine for bundling. Meanwhile, heavier materials, including hard plastics, textiles, rubber, and large organic waste, are also packed and held for further processing.